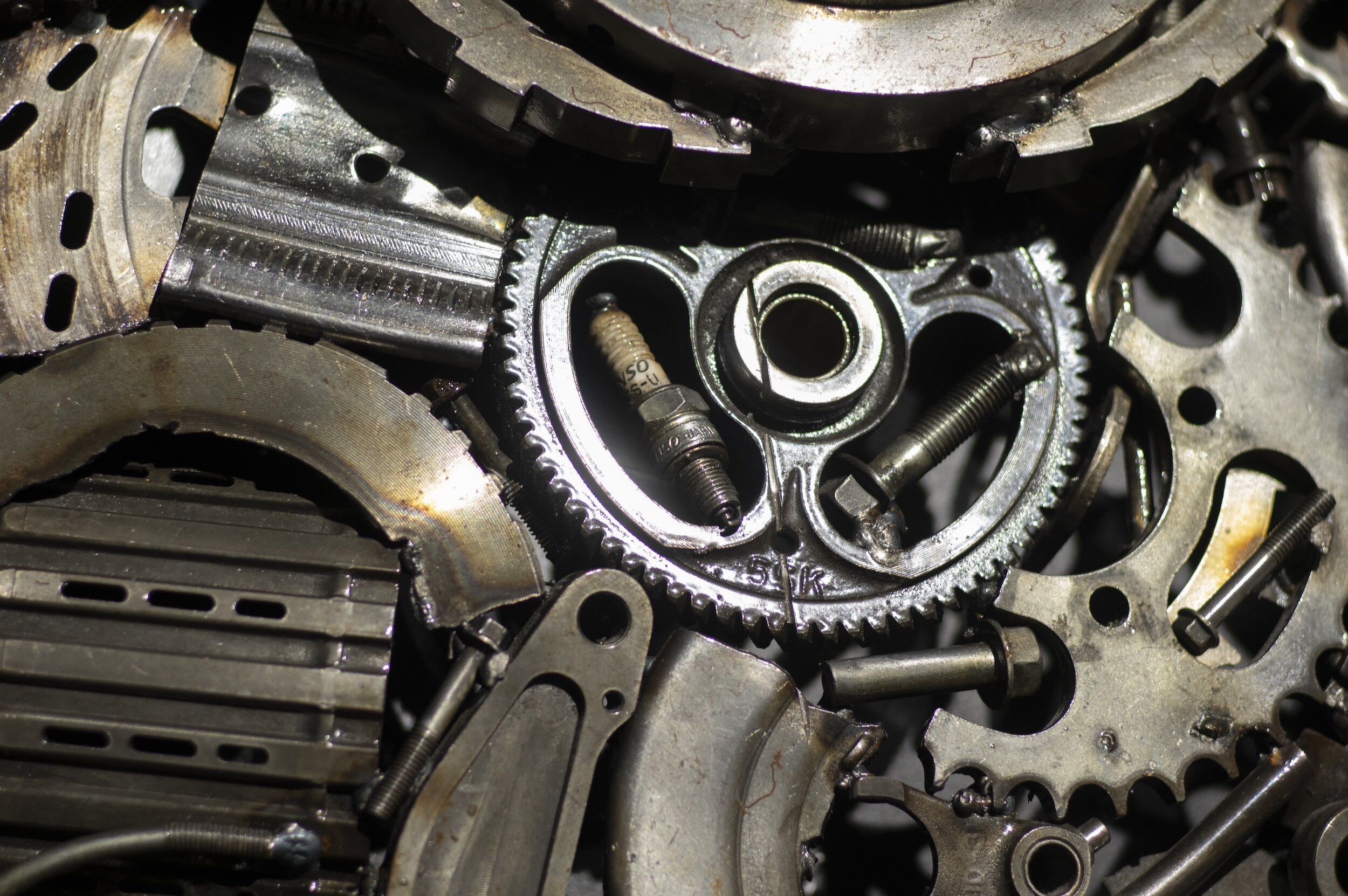
Our Process
Our Vapor Blasting Process
Our vapor blasting technique is a testament to our keen precision, revealing the true beauty beneath layers of wear and tear. Through the use of advanced vapor blasting equipment, we utilize a mixture of water, abrasive media, and compressed air to a achieve superior finish. After spending years honing our skill, we’ve built a solid reputation for high quality finished products that are done on time. Over time, we’ve developed our 3-step process to achieve the best vapor blasting results.
Step 1: Prep Work
Arnold’s design takes the absolutely necessary time to painstakingly prep each piece, including any light cleaning. Here is an example of how a cylinder might look when it comes into the shop. This particular piece was sent in pre-cleaned, which we greatly appreciated but don’t require. It had also been bead-blasted by someone else, which left the part with a satin finish that wasn’t quite special enough for the customer. They sent us the part to be vapor blasted to let the true beauty of the part shine.
Click to enlarge.
Step 2: Deoxidizing
The second critical step in the process involves deoxidizing the part. Old aluminum parts become encased in aluminum oxide over time, especially parts exposed to weather. Aluminum oxide rates a 9 on Mohs scale of hardness. (With talcum being at 1 and diamond at 10 on this scale, you can imagine just how stubborn this can be to remove.) Glass beads are 5.5 on Mohs scale; not quite hard enough to break through thick oxide layers for effective finishing. That’s why we use micro beads- they’re hard enough to penetrate the aluminum oxide buildup without causing any damage to the actual part.
The same part after masking and deoxidizing.
Click to enlarge.
Step 3: Vapor Blasting
Lastly is the actual vapor blasting stage. This is where the parts are proofed. Sometimes we will repeat the previous step if we don't think the finish is good enough due to some lingering oxides. Only when the part is bright and velvety do we do the final rinse and dry. After that, each surface of the part is thoroughly inspected to check for finish uniformity. Once the part has been perfected, we package it up and send it back to you! Though this last step can be very time-consuming, its critical to achieving the best and most uniform finish possible for your part.
Click to enlarge.
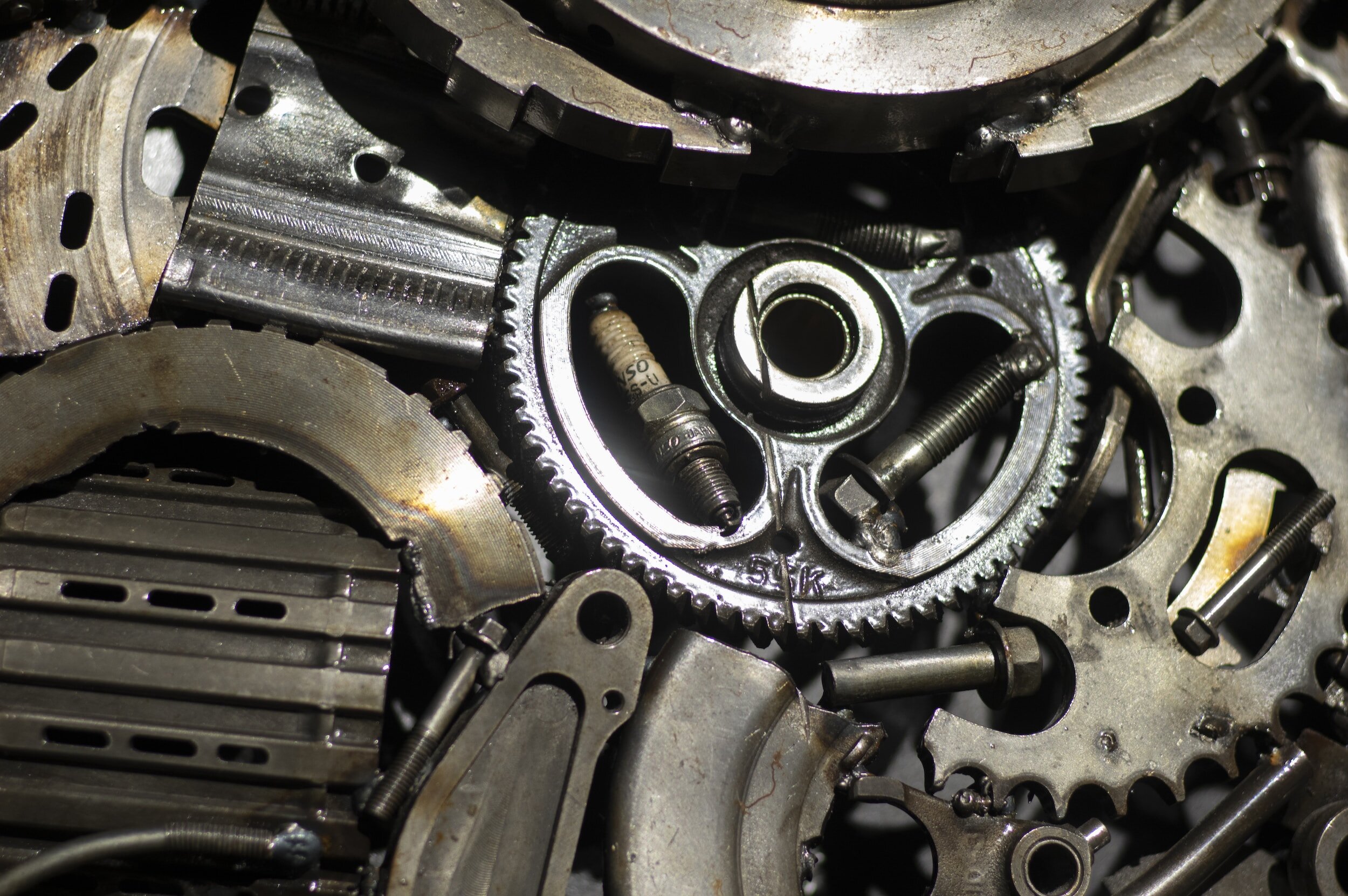
But Can’t I Just Use Soda Blasting?
Every so often, we come across someone recommending soda blasting in place of vapor blasting to get the same finish. This is incorrect. To be fair, soda blasting is a great medium for cleaning. It is very good for thin parts too, because it doesn't build up heat and warp the part.
However, it simply doesn't have the physical characteristics and hardness necessary to cut through heavy oxide layers and leave a satin finish like with vapor blasting. Customer’s are always welcome to have their parts blasted before sending them to us. Sometimes we even encourage it! But it’s still very likely that oxides will need to be removed once we receive your part still. If you’re not sure. you’re always welcome to email us to see what the best option is at b.arnold@arnoldsdesign.com.